The Fatal Four: Prolific hazards in the construction industry
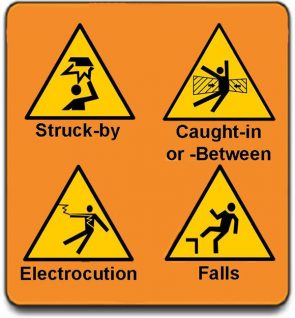
Introduction
Construction sites expose workers to a plethora of potential hazards however, there are four that OSHA has labeled as the Fatal Four. These four hazards account for the majority of injury and death (63.7% in FY 2016) among construction workers and account for over 21% of total deaths in private industry.
What are the Fatal Four?
The Occupational Safety & Health Administration (OSHA) has identified the four leading causes of fatalities in the construction industry – known as OSHA’s “Fatal Four Hazards” or “Construction Focus Four Hazards”.
The Fatal Four consist of falls, electrical exposure, struck-by and caught-in/between situations, and resulted in 545 worker fatalities in the United States in FY 2016. The Bureau of Labor Statistics (BLS) estimate that 631 workers’ lives would be saved in America every year by eliminating the Fatal Four. While this is easier said than done, it is absolutely possible to reduce and eventually eliminate these fatal four hazards on your jobsite if you and your employees know what to look out for.
Fall Hazards
Listed as the #1 most frequently cited OSHA standards violation in FY 2017 was fall protection in the construction industry. Unfortunately, this is not the first time fall protection has been cited on this OSHA list. In fact, it’s been cited as the #1 violation for 7 years running!
The importance of fall protection
It should be glaringly obvious that falls are among the most common causes of serious work related injury and/or deaths. Falling from overhead platforms, elevated work stations or into holes in the floor and/or walls can be prevented when an employer provides the proper equipment and training to their employees.
Reducing falls on the jobsite
Working at elevations exceeding four feet in general industry, five feet in shipyards, six feet in the construction industry and eight feet in longshoring operations, OSHA requires that fall protection be provided to workers. In addition, OSHA requires fall protection for any worker engaged in work activities that are above dangerous equipment and machinery, regardless of the fall distance. For more resources on fall protection, check out OSHA’s reference materials.
OSHA’s minimum requirements for employers to prevent injuries from falls:
- Guard every floor hole using a railing and toe-board or a floor hole cover to prevent a worker accidentally walking into the hazard.
- Guardrails and toe-boards must be provided around every elevated open sided platform, floor or runway.
- Employers must provide guardrails and toe-boards to prevent workers from falling and getting injured by dangerous machines or equipment, regardless of height.
- Safety harness and line, safety nets, stair railings and handrails are some of the other means of fall protection that may be required on certain job sites.
Additional OSHA requirements for employers:
- Provide working conditions free from known dangers.
- Keep floors in work areas in a clean and, so far as possible, a dry condition.
- Select and provide required personal protective equipment (PPE) at no cost to workers.
- Train workers about job hazards in a language that they can understand.
Electrical Hazards
Electricity has long been considered a serious workplace hazard. OSHA’s electrical standards are designed to protect workers exposed to dangers such as electric shock, electrocution, fires and explosions. The Bureau of Labor Statistics (BLS) estimates that 52% of all electrical fatalities in the U.S. workplace are in the construction industry. Most of which were caused workers directly contacting overhead power lines, machines, tools and hand-carried metallic objects.
Who is at risk?
Professionals who are exposed to the most risk for electrical hazards include overhead line workers, electricians and engineers. Common tasks that put them at risk include electrical installation and repairs, testing of fixtures and equipment and inspection and maintenance activities. In addition, people who are indirectly working with electricity are also exposed to electrical hazards including office workers.
Most common electrical hazards on the job site
- Overhead Power Lines –
Overhead electrical lines that are energized carry high voltages that cause major burns and electrocution to workers who come in contact with them. Workers and equipment should maintain a 10 ft. distance from energized lines. Site surveys should be conducted to ensure nothing is stored beneath overhead lines and safety barriers and signs must be installed to warn nearby workers of the hazards present in the work site. - Damaged Tools and Equipment –
Thoroughly check for cracks, cuts or abrasions on cables, wires and cords. Identify all defects and have them repaired or replaced before using the equipment. Before beginning electrical maintenance and repairs, Lock Out/Tag Out procedures must be performed. - Overloaded Circuits & Improper Wiring –
Use the correct wire for the operation and the electrical load to work on. Using wires with incorrect size for the current can cause overheating and fires. Also use the correct extension cord designed for heavy duty use. Perform regular fire risk assessments to identify areas at risk of bad wiring and circuits. - Exposed Electrical Parts –
These hazards can cause potential shocks and burns. Always check for and exposed parts and properly guard mechanisms. Repair all equipment immediately if any defects are found. - Improper Grounding –
Improper grounding of equipment is OSHA’s #1 electrical violation. Proper grounding of equipment eliminates unwanted voltage and reduces the risk of electrocution. - Damaged Insulation –
Defective insulation is a hazard that everyone should be able to identify and report immediately. Power should be turned off before replacing damaged insulation and should never be covered with electrical tape. - Wet Conditions –
Electrical equipment should never be operated in wet conditions. A qualified electrician should be consulted to inspect electrical equipment that has been exposed to moisture before you energize the equipment.
Using a checklist to remember these points can be easier than relying on memory alone. Check out OSHA’s Electrical Hazard Checklist to help you identify hazards on your job site.
Struck-by Hazards
Our examination of the Fatal Four continues with struck-by-hazards. According to the latest data by OSHA, in FY 2016 struck-by hazards accounted for 9.4% of the total deaths in construction; second only to fall hazards. Struck-by hazards occur when a worker comes into forceful contact with a flying, falling, swinging or rolling object.
Struck-by Flying Objects
When something has been thrown, hurled or is being propelled across space, a flying object hazard exists. Instances resulting in injuries or fatalities can happen when material separates from a tool, machine or other equipment, striking a worker. An object can also be ejected under power by a tool such as a nail gun. Commonly used in power tools, compressed air can also cause flying object hazards.
Struck-by Falling Objects
A worker can be crushed, pinned or caught under an object that fell from elevation to a lower level. There are many situations that relate to this hazard and it’s difficult to prepare for all the possibilities.
However, you can take some simple measures such as barricading work zones to prevent entry where equipment is operating or the work is being performed overhead. You can also barricade or seperate any work tasks that create flying debris to protect workers against exposure. Removing tools and unnecessary materials from elevated locations will eliminate the hazard they present. If you must leave tools or materials at elevation, make sure the proper toe-boards are in place to prevent materials slipping or tie off your materials to ensure they do not fall to a lower level.
Again, it’s difficult to guard against all the possible hazards for a falling object, but you can help to eliminate exposure to these risks by planning and defining your work zones.
Struck-by Swinging Objects
Swinging objects can result from a load being mechanically lifted around a worker. When loads are lifted, they have a tendency to twist and swing; especially in windy conditions. This movement can catch a worker off guard and they could be hit by a swinging load. In addition, swinging loads can result in improper rigging techniques; loads must always be properly rigged to prevent slippage.
Swinging objects can also include objects which are not free standing and they are attached at some point or are being held by the worker. A hinge-like motion can occur, causing the worker to be struck-by a slamming or swinging motion of an object.
Struck-by Rolling Objects
An object that is rolling, moving or sliding on the same level as the worker can cause a struck-by rolling object incident. This can include situations in which a worker is struck by a moving vehicle without being caught under it. This can also result from a worker being struck-by a sliding object or equipment on the same level.
Caught-in or Between Hazards
Making a determination between a Caught event and a Struck event comes down to one key factor, whether the impact of the object alone caused the injury. When the injury is created more as a result of crushing injuries between objects, the event should be recorded as Caught.The event should be recorded as Struck when the impact of the object alone creates the injury.
Trenching Hazards
There were almost twice as many fatalities from trenching and excavation incidents in 2016 compared to the average over the past five years. In 2018, this trend is continuing at the same time OSHA is making efforts to reduce the number of incidents by increasing awareness of the hazards and educate employers and workers on how to prevent cave-ins and trench collapses.
Any trench that is deeper than 5 ft. must have protective systems in place and any trench deeper than 20 ft. must have a professional engineer design the protective system.
A competent person, at your work site, must be trained to the OSHA standard regarding the use of protective systems and soil classifications. Their responsibilities include identifying and eliminating hazards before any worker enters the trench or excavation area and while work is being performed.
Power Tool & Machinery Hazards
- Only operate machinery when using the proper safety guards.
- Never wear loose clothing or jewelry around moving parts of tools.
- Always properly Lock Out/Tag Out all equipment to avoid accidental activation.