Machine Guarding 101 – The Basics
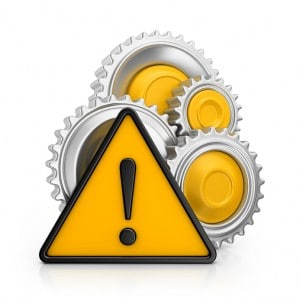
Introduction
Machines with moving parts present many potential hazards to workers who operate them. Crushed fingers or hands, amputations, burns and blindness are just some of the potential hazards that can occur when a machine guarding is not properly installed. Any machine part, function or process that may cause injury must be safeguarded.
Hazardous Mechanical Motions and Actions
There are a wide array of mechanical motions and actions that present hazards to workers. Below we will explore, in detail, the basic types of hazardous mechanical motions and actions.
Motions
Rotating: Rotating mechanisms which may be hazardous include cams, collars, clutches, flywheels, spindles and meshing gears. The danger increases when projections such as screws, bolts, nicks or abrasions are exposed on rotating parts.
Pinch Points: This danger is common on machines with intermeshing gears and rolling mills. Pinch points can also occur between rotating and fixed parts creating a shearing or crushing action.
Reciprocating motions: The up-and-down or back-and-forth motions can cause a worker to be struck by or caught between moving and stationary parts.
Transverse motions: The movement in a straight or continuous line can strike a worker or cause them to get caught in a pinch or shear point by the moving part.
Actions
Cutting: Cutting action dangers exist at the point of operation where finger, arm and body injuries can occur and where flying chips of material can strike the head, eyes, or face. These hazards are present at the point of operation when cutting woods, metals or other materials.
Punching: When power is applied to a slide (ram) for the purpose of blanking, drawing, or stamping metal or other materials, punching hazards are created. This hazard also occurs at the point of operation where stock is inserted, held and withdrawn by hand.
Shearing: This action involves applying power to a slide or knife in order to trim or shear metal or other materials. A hazard occurs at the point of operation where stock is inserted, held and withdrawn.
Bending: When power is applied to a slide in order to draw or stamp metal or other materials, a bending action results. Again, a hazard occurs at the point of operation where stock is inserted, held and withdrawn.
Safeguard Requirements
Safeguards must meet the following general requirements to protect workers against mechanical hazards.
Prevent Contact: A good safeguarding system eliminates the possibility of the operator placing parts of their bodies near hazardous moving parts.
Secure: Operators should not be able to easily remove or tamper with the safeguard. An ineffective safeguard is as good as no safeguard at all.
Protect from falling objects: Safeguards should ensure that no falling object can come in contact with moving parts.
Create no new hazards: If a safeguard creates a hazard of its own such as a shear point, it defeats its own purpose.
Create no interference: A safeguard will quickly be overridden or disregarded if it impedes a worker from performing the job quickly and comfortably. Enhance efficiency and relieve the worker’s apprehensions with proper safeguarding.
Allow safe lubrication: An operator should be able to lubricate a machine without removing safeguards. Locating oil reservoirs outside the guard will reduce the need for the operator or maintenance worker to enter the hazardous area.
Training
No safeguards are effective unless the operator knows how and why to use it. Training is a crucial part of any effort to provide safeguarding against machine-related hazards. Operator training should involve instruction and hands-on training in the following areas:
- Description and identification of the hazards associated with specific machines
- How the safeguards provide protection and identify the hazards for which they are intended
- How and why to use safeguards
- Under what circumstances safeguards can be removed
- What to do if a safeguard is damaged, missing or unable to provide proper protection
This kind of safety training is necessary for new operators and maintenance or setup personnel, when any new or altered safeguards are put in service, or when workers are assigned to a new machine or operation.
PPE
Engineering controls must be the first choice for eliminating machine hazards. But when those controls are not available or do not fully protect the worker, operators must wear protective clothing or personal protective equipment.
Always choose the protective clothing and equipment that is:
- Appropriate for the specific hazard
- Maintained in good condition
- Properly stored when not in use
- Kept clean, fully functional and sanitary
PPE is available for different parts of the body. You can see OSHA’s resource on PPE to help you choose the proper protection for the machine you’re operating.
Also check out our Safety Talks installment on Machine Guarding here.