Improving the Safety of Your Chemical Management System: A Guide
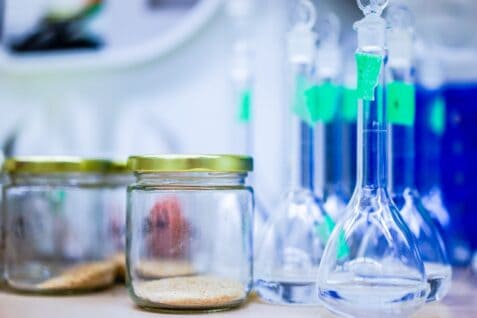
Effective chemical management and safety practices are paramount in any organization that handles or stores chemicals. The consequences of inadequate chemical safety can be severe, ranging from accidents that endanger lives to regulatory penalties that can cripple businesses.
In an era where environmental concerns and workplace safety are in the spotlight, it is crucial for organizations to take proactive steps to ensure the safety of their chemical management systems.
By the time you finish reading this article, you will have the knowledge and tools necessary to build a robust chemical management system that not only ensures safety and compliance but also contributes to a healthier workplace and environment.
Together, we can make our workplaces and communities safer and more secure in the face of the complex challenges presented by chemical hazards.
Chemical Hazards
Chemical hazards are diverse and must be precisely identified and categorized. This involves recognizing various types of hazards, including toxicity, flammability, reactivity, and environmental harm.
Identifying chemical properties and reviewing Safety Data Sheets (SDS) provides critical insights into the nature of chemical hazards.
Identifying and Categorizing Chemical Hazards
Identification of chemical hazards is a fundamental step in safe chemical management. These hazards encompass a range of characteristics, from the potential to cause harm to the environment, to risks associated with fire and explosions.
By discerning these hazards, organizations can make informed decisions regarding the safe storage, handling, and disposal of chemicals.
The Importance of Chemical Safety Data Sheets (SDS)
Chemical Safety Data Sheets (SDS), previously known as Material Safety Data Sheets (MSDS), serve as indispensable references in chemical management. These documents provide comprehensive information about a chemical’s properties and potential hazards.
An SDS typically includes details regarding a chemical’s composition, physical and chemical attributes, health and environmental risks, as well as recommended procedures for safe handling and responding to emergencies.
Common Chemical Safety Symbols and Labels
Effective communication about chemical hazards relies on standardized symbols and labels. Manufacturers and suppliers use these visual cues to convey critical information about a chemical’s properties and risks.
Understanding these common symbols and labels is essential for those working with chemicals. These visual cues quickly provide information that is vital for safe handling and storage.
Legal and Regulatory Framework
Organizations that handle chemicals are subject to a comprehensive array of regulations and standards. These regulatory frameworks originate from various levels of government, including federal, state, and local authorities.
They are designed to ensure the safe management of chemicals and mitigate associated risks.
Additionally, industry-specific organizations may establish standards tailored to specific sectors, adding another layer of complexity to compliance.
Key Areas of Regulation
The regulations encompass a wide range of critical areas. Let’s take a look at these now.
Chemical Labeling
Requirements for accurate labeling to inform personnel of chemical hazards and usage.
Storage Requirements
Guidelines for safe and secure chemical storage, addressing issues such as compatibility and containment.
Transportation Guidelines
Regulations governing the safe transportation of chemicals to prevent accidents and environmental contamination.
Permissible Exposure Limits (PELs)
Establishing exposure limits to protect workers from harmful chemical concentrations.
Understanding these regulations and staying updated on any changes is vital for achieving compliance, ensuring the safety of personnel, and preventing environmental damage.
Understanding Compliance Requirements
Ensuring compliance is absolutely vital for any company working with chemicals. It is important for both employee safety reasons, and because the financial price of non-compliance can be very high.
Beyond Paperwork
Compliance with chemical management regulations is not a mere matter of bureaucratic paperwork. It demands a comprehensive grasp of the specific requirements that apply to your organization’s activities. These requirements typically extend beyond documentation and may encompass:
Documentation
Organizations must maintain detailed records related to chemical handling, including material safety data sheets (SDS), training records, and incident reports.
Reporting Procedures
Compliance often necessitates the timely and accurate reporting of chemical-related incidents, ensuring that the appropriate authorities are informed in the event of accidents or spills.
Employee Training
Personnel must receive adequate training to understand the hazards associated with chemicals they handle and know how to respond to emergencies effectively.
Safety Measures
Organizations are expected to implement safety measures and protocols to minimize risks associated with chemical management.
Adhering to these obligations is essential for preventing chemical accidents, safeguarding the environment, and maintaining a secure chemical management system.
Penalties for Non-Compliance
Non-compliance with chemical management regulations can lead to severe legal and operational consequences.
Organizations that fail to meet their legal obligations may face the following consequences.
Hefty Fines
Regulatory authorities may impose substantial fines for non-compliance, which can significantly impact an organization’s financial stability.
Legal Action
Non-compliance can result in legal actions, including lawsuits and injunctions, which can further damage an organization’s reputation and finances.
Business Disruption
In some cases, non-compliance may lead to the suspension or closure of business operations until corrective actions are taken and compliance is achieved.
Reputation Damage
Public perception and trust can be eroded, causing long-term damage to an organization’s reputation.
Organizations must proactively prioritize compliance with regulations and standards to ensure the safety of their personnel and the broader community while mitigating these potential legal and reputational risks.
Assessing Your Current System
Begin your journey toward a safer chemical management system by taking a close look at your current processes and protocols.
A thorough evaluation of your existing system is the foundation upon which improvements are built.
This evaluation involves examining every aspect of how you handle and store chemicals, from the moment they arrive at your facility to their ultimate disposal.
Identifying Strengths and Weaknesses
During the evaluation, identify the strengths and weaknesses of your current system. What are you doing well? Which aspects of your chemical management system are effective, compliant, and protective of your personnel and the environment?
Conversely, where are the vulnerabilities? Are there areas where safety protocols fall short, or where compliance with regulations is uncertain?
Recognizing these strengths and weaknesses provides a roadmap for the changes you need to make.
Gathering Data on Chemicals in Use
Comprehensive data on the chemicals you use is an integral part of the assessment. This includes not only the types and quantities of chemicals but also their specific properties and hazards.
This data is crucial for identifying potential risks, determining appropriate storage and handling procedures, and ensuring compliance with regulations.
By collecting and maintaining accurate and up-to-date information about the chemicals in use, you empower your organization to make informed decisions about their management.
Chemical Storage and Handling
Safe storage is an absolute cornerstone for ensuring the well-being of personnel and the environment. Adhering to best practices in chemical storage is paramount to prevent accidents and protect against potential hazards.
One of the critical considerations in chemical storage is compatibility. This entails segregating chemicals to prevent any contact between incompatible substances that could lead to dangerous reactions. Additionally, proper containment is essential.
Chemicals should be stored in containers that prevent leaks or spills, minimizing the risk of exposure. Adequate ventilation is another vital aspect of safe storage, as it helps disperse potentially harmful vapors.
Maintaining the right temperature conditions is crucial to prevent thermal reactions, which can be catastrophic.
Guidelines for Handling and Transporting Chemicals
Guidelines for the proper handling and transportation of chemicals are fundamental to ensuring safety throughout their life cycle. These procedures encompass various aspects of chemical management, including the use of personal protective equipment (PPE) for personnel involved in handling chemicals.
Ensuring that individuals wear appropriate protective gear, such as gloves and goggles, is essential to minimize exposure risks. Equally important is the use of secure containers designed for the safe transport of chemicals. Proper sealing and labeling are critical to prevent accidents during transportation.
Having well-defined spill response procedures and training personnel to enact them effectively is vital to reducing the consequences of accidental chemical spills. Safe handling and transport practices are essential for minimizing risks associated with chemical management.
Proper Labeling and Signage
Clear and accurate labeling and signage are key components of chemical safety. This involves marking chemical containers with essential information, such as the chemical’s name, hazard warnings, and instructions for safe usage.
Effective labeling ensures that individuals can quickly and accurately identify the substances they are working with, helping prevent mix-ups and errors. Moreover, providing emergency information, including contact details and instructions for immediate actions in the event of chemical exposure or spills, is critical for rapid response and minimizing the impact of accidents.
Signage plays a significant role in guiding personnel within a facility, helping them identify areas with chemical hazards, locate fire exits, find eyewash stations, and access safety equipment quickly in emergencies.
Proper labeling and signage are essential elements of a safe and compliant chemical management system, contributing to the protection of individuals and the environment.
Risk Assessment and Mitigation
A fundamental step in achieving a safe chemical management system is conducting a comprehensive risk assessment. Risk assessment involves identifying and evaluating potential hazards associated with the chemicals in use, as well as the processes, equipment, and environments where these chemicals are handled.
It is a structured process that requires a thorough understanding of the chemicals’ properties and behaviors, potential exposure pathways, and the consequences of accidents or mishandling.
By systematically assessing risks, organizations can pinpoint areas of concern and prioritize measures to mitigate those risks effectively.
Strategies for Minimizing Chemical Risks
Once potential risks are identified through the risk assessment, organizations can then develop and implement strategies for minimizing these risks. This involves employing a range of safety measures and controls, which may include:
- Substituting hazardous chemicals with less hazardous alternatives
- Implementing engineering controls
- Enforcing administrative controls
- Providing personal protective equipment (PPE)
- Regularly inspecting and maintaining equipment and storage facilities
The goal of these strategies is to create a layered approach to risk reduction, minimizing the potential for accidents and ensuring a safe working environment for all personnel.
Emergency Response Planning
Despite the best precautions, the possibility of chemical incidents always exists. Emergency response planning is essential to mitigate the consequences of such incidents.
Organizations should develop and implement detailed emergency response plans that outline how to respond to chemical spills, leaks, fires, or exposure incidents. These plans should encompass:
- Clear roles and responsibilities for emergency responders.
- Procedures for evacuating personnel safely.
- Protocols for containing and managing chemical spills or releases.
- Information on the use of safety equipment
- Communication plans for alerting and informing relevant parties
The effectiveness of an emergency response plan depends on regular training and drills to ensure that personnel are familiar with the procedures and can respond swiftly and effectively in the event of a chemical incident.
Emergency response planning is a critical component of a comprehensive chemical management system, designed to safeguard lives, protect the environment, and minimize the impact of unexpected chemical events.
Training and Education
Ensuring that personnel are well-versed in the hazards associated with chemicals, the safe handling procedures, and emergency response protocols is of paramount importance. The significance of employee training extends far beyond mere compliance; it is central to mitigating risks, preventing accidents, and protecting lives.
Chemical incidents can have devastating consequences, ranging from minor mishaps to catastrophic disasters. Proper training equips employees with the knowledge and skills necessary to recognize and respond to potential chemical hazards.
It empowers them to take appropriate precautions, work safely, and act swiftly in the event of an emergency. Well-trained personnel are more likely to make informed decisions that reduce risks. This ensures the safety of themselves, their colleagues, and the environment.
Creating a Culture of Safety
Training and education are not isolated events but integral components of fostering a culture of safety within an organization. A culture of safety places the well-being of personnel and the environment at the forefront of all activities, and it starts with leadership.
Managers and supervisors must champion a commitment to safety, setting an example for others to follow. This involves creating an environment where safety is not just a priority but a shared value.
When employees perceive safety as a core organizational value, they are more likely to embrace training and actively participate in safety programs. A safety culture encourages open communication, where employees feel comfortable reporting concerns and near misses without fear of reprisal.
It prioritizes ongoing improvement, regularly evaluating and updating safety procedures to adapt to changing circumstances and emerging risks.
Continuous Education and Awareness
Education and training are not static processes; they require ongoing commitment and awareness. Chemical hazards, regulations, and safety best practices evolve over time.
Organizations must provide continuous education to keep their personnel up-to-date with the latest knowledge and methods. This includes regular refresher courses, updates on regulatory changes, and sharing lessons learned from past incidents.
Promoting awareness about chemical hazards and safety should extend beyond formal training sessions. Organizations can foster an environment where employees are encouraged to stay vigilant and share their knowledge with colleagues.
Safety reminders, posters, and regular safety meetings can serve as consistent sources of awareness. By promoting a culture of safety that encourages ongoing education and awareness, organizations not only prevent accidents but also create a workplace where every individual feels responsible for safety.
This will ultimately enhance the overall well-being and security of the workforce and the environment.
Record Keeping and Documentation: The Vital Role of Safety Data Sheets (SDS)
Within the landscape of chemical management, Safety Data Sheets (SDS) play an exceptionally pivotal role. SDS are not just paperwork or documents. They are a comprehensive repository of critical information about chemicals, encompassing their properties, hazards, safe handling procedures, and emergency response guidance.
These sheets provide a wealth of knowledge that is indispensable for the safe management of chemicals.
They serve as the principal reference point for understanding the substances in use, and are pivotal in creating a secure and responsible chemical management system.
Maintaining Accurate and Comprehensive SDS
Accurate and up-to-date SDS are a foundational component of chemical management. Organizations are not only responsible for obtaining SDS from chemical suppliers but also for maintaining them in a systematic and organized manner.
This requires vigilance in keeping these documents current, as they must reflect the latest information available. Any updates or changes in the chemical composition, properties, or hazards must be promptly reflected in the SDS.
Maintaining an SDS library serves several vital functions. Firstly, it equips personnel with the knowledge they need to work with chemicals safely. This includes understanding the potential risks, required safety measures, and appropriate response in case of exposure or accidents.
Secondly, comprehensive and accurate SDS are a cornerstone for risk assessment, helping organizations identify potential hazards and assess their associated risks.
This is vital for developing safety protocols and making informed decisions in chemical management.
Incident Reporting and SDS
The crucial role of SDS extends to incident reporting and documentation. In the event of a chemical incident, SDS serve as a vital resource for evaluating the hazards posed by the substances involved and determining the most appropriate response.
Incident reports should reference the relevant SDS, as they provide the foundational data needed to understand the chemical properties and related risks.
Record Retention and Accessibility
Record retention, particularly with regard to SDS, is essential for ongoing safety and regulatory compliance. SDS should be retained for as long as the chemicals are in use and beyond.
The duration of retention may be dictated by regulations or specific organizational policies. This ensures that personnel always have access to the most recent information about the chemicals they work with.
Accessibility to SDS is critical. Personnel handling chemicals should have easy and immediate access to these documents.
This availability empowers them to make informed decisions, respond to chemical incidents, and ensure their safety, as well as the safety of their colleagues and the environment.
Emergency Response and Preparedness: A Pillar of Chemical Management
A comprehensive emergency response plan is an essential component of chemical management. It is a structured and systematic approach to address potential chemical incidents, accidents, or disasters that can have far-reaching consequences for personnel, the environment, and the organization.
The development of such a plan involves careful assessment of the risks associated with chemical operations, and the formulation of strategies to mitigate these risks.
Key elements of an effective emergency response plan include:
- Identification of potential chemical hazards and risks.
- Clarity on the chain of command and reporting procedures.
- Protocols for evacuating personnel safely.
- Procedures for containment and management of chemical spills or releases.
- Communication strategies for alerting and informing relevant parties, including authorities and emergency services.
Employee Roles and Responsibilities during Emergencies
During an emergency, it is essential to have clearly defined roles and responsibilities for employees. Each member of the organization must understand their role and know how to respond effectively. This includes:
- Evacuation procedures.
- Proper use of safety equipment, such as fire extinguishers or safety showers.
- Reporting incidents promptly to the appropriate authorities.
- Providing assistance to colleagues who may be injured or in distress.
Effective communication is at the core of employee responsibilities during an emergency. Personnel should know how to report incidents, raise alarms, and convey critical information to both colleagues and external responders.
Clarity on these roles and responsibilities is instrumental in coordinating efforts and ensuring a swift and effective response.
Conducting Regular Drills and Simulations
The effectiveness of an emergency response plan hinges on regular drills and simulations.
These exercises replicate various emergency scenarios, allowing personnel to practice their roles, familiarize themselves with safety equipment, and test the procedures outlined in the response plan.
Regular drills help identify any gaps or shortcomings in the plan, facilitating its refinement and ensuring that all personnel are well-prepared in the event of a real emergency.
Improve Your Chemical Management System Today
KHA is committed to enhancing your chemical management system’s safety and efficiency. Our team of safety data sheet experts is dedicated to delivering top-notch services that align with your unique needs.
With years of experience, we understand the importance of compliance, risk mitigation, and accurate SDS when handling chemicals. Whether it’s creating robust emergency response plans, ensuring regulatory adherence, or optimizing your chemical inventory, we have you covered.
Contact KHA today to discuss your specific requirements.