Are SDS Sheets Required by Law?
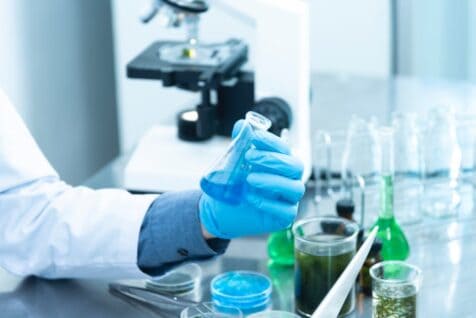
Chemicals are frequently manufactured and distributed to other manufacturers for use in various products. When these chemicals are used correctly, they pose no harm. When used incorrectly, however, they can cause serious injury and even death.
This is why when a chemical manufacturer distributes its product to another manufacturer, it’s important for it to send along SDS sheets. SDS sheets are safety data sheets. These are integral to hazard communication, as they enable users of chemicals to gain a thorough understanding of said chemicals before using them.
What you might be wondering, though, is whether SDS sheets are required by law. And, if they are, what are the specifics of SDS regulations? We’re going to get into all of this below, highlighting the particulars of OSHA SDS requirements.
Ready? Let’s get started!
Are SDS Sheets Legally Required?
Let’s get into the big question: are SDS sheets legally required? As long as a product contains a potentially dangerous chemical, then yes, an SDS sheet needs to be submitted along with it.
When a supplier distributes a chemical-containing product, it must send along an SDS sheet for the product as well. When a manufacturer uses that product in the manufacture of one or more of its goods, it must keep the relevant SDS sheet catalogued in a journal or database in the direct workspace.
In essence, if you work with hazardous chemicals on any basis, then, yes, you need to post SDS sheets. Doing so is required by law.
Where Do SDS Sheets Need to Be Posted?
SDS sheets need to be posted in any work area in which potentially dangerous chemicals are being used. They must be immediately available to workers in those areas through either physical or digital means.
Note, SDS sheets can not be in a room separate from where work is being done. They must be in the same area where workers are handling the potentially dangerous chemicals.
This is vital, as the ability to quickly access SDS sheets is imperative. In given situations, if you’re not able to access SDS sheets, undue injury or even death could be suffered.
Rules for Complying With SDS Laws
To comply with SDS laws, there are a number of criteria that you need to meet. These include the following:
Ensure That SDS Sheets Are Readily Accessible to Employees
First and foremost, you need to ensure that your SDS sheets are readily accessible to your employees. Not only should they know how to access them but they should also be able to access them within their direct work area.
To help meet this criterion, it’s vital for you to educate your employees during the onboarding process. Show them not only where SDS sheets are located but how to read and understand them as well. If they’re digital in nature, make sure your employees know how to use the digital system.
Ensure That SDS Sheets Are Written Correctly
Not only do SDS sheets need to be present in the direct work area but they also need to be written correctly. If they’re missing information, they might not convey what they need to convey. This could put your employees in dangerous situations.
Therefore, when writing SDS sheets, it’s important to follow the guidelines provided by OSHA. You can find these guidelines at this link.
Ensure That SDS Sheets Are Updated
Over time, the chemical information associated with a product can change. Therefore, SDS sheets need to be reviewed and updated every 3 years. If they’re not updated in a timely manner, they’ll be considered invalid and could therefore result in fines.
This is why it’s vital to systematize your SDS process. Maintain a maintenance schedule to ensure that you’re updating your sheets as needed. If you need assistance with the process, consider outsourcing it to an SDS sheet management company.
Penalties for Not Complying With SDS Laws
Now, you might be wondering: what are the penalties for those companies that don’t comply with SDS laws? Generally speaking, they come in the form of fines. If, during an OSHA inspection, it’s found that you don’t have SDS sheets properly posted, you’ll have to pay a fine for each citation.
The amount of the fine can vary based on a variety of factors. That said, the maximum fine for such an offense is $7,000.
You don’t want to have to pay out thousands of dollars simply because you failed to properly adhere to SDS laws. So, follow the protocol and ensure that you’re doing things by the book.
Which Substances Require SDS Sheets?
Next, we’re going to discuss the substances that require SDS sheets. In general, they’re substances that have the potential to cause physical harm to those around them.
If a chemical possesses one of the following characteristics, it undoubtedly requires an SDS sheet. Note: there are other characteristics that can trigger the need for an SDS sheet as well. If you have any questions about specific chemicals, you should contact OSHA directly.
Explosive
Does the chemical have the potential to explode when mixed with other chemicals? Could exposure to fire cause it to explode? If so, it needs to come with an SDS sheet.
Flammable
It’s not just explosive substances that need SDS sheets. Flammable substances need them as well. These count as substances that are especially prone to catching on fire.
Self-heating
Are you dealing with a substance or product that has the ability to heat itself upon the introduction of a certain action? For instance, you might be dealing with self-heating food packaging or self-heating socks. If so, an SDS sheet is required.
Self-reactive
Self-reactive chemicals need to be equipped with SDS sheets as well. These are chemicals that explode or ignite when they reach certain temperatures. An example would be Azo compounds.
Pyrophoric
A pyrophoric substance is a substance with the potential to ignite spontaneously upon making contact with air. An example would be triethylborane, a chemical used in the manufacture of pharmaceuticals. All pyrophoric chemicals must come with SDS sheets attached.
Corrosive
Corrosive chemicals need to have SDS sheets also. These are chemicals that eat through metal and other solid substances. They run the gamut from bathroom cleaning agents to sulfuric acid and everything in between.
Containing Pressurized Gas
When pressurized, gas has the potential to lead to an explosion. For this reason, all pressurized gas products must come with SDS sheets attached.
Acutely Toxic
Acute toxicity describes a chemical situation where short-term exposure leads to a quick and severe reaction. For instance, you might touch sulfuric acid once and get instant burns on your hands. All acutely toxic chemicals are highly dangerous and therefore need to have SDS sheets attached to them in workspaces.
Skin Irritating
Chemicals that irritate the skin need to come with SDS sheets as well. These include everything from drain cleaners to furniture waxes to fragrance sprays and more.
Carcinogenic
A carcinogenic chemical is a chemical with the potential to cause cancer. A great many chemicals are carcinogenic in nature, including nickel, benzidine, and cadmium. If dealing with these chemicals, make sure to post SDS sheets for them.
Toxic to the Reproductive System
There are also chemicals that are toxic to the reproductive system. These chemicals can cause fertility issues, and include everything from lead to anesthetic gases and more. These too need to come with SDS sheets attached.
A Hazard for Aspiration
An aspiration hazard is a chemical with the potential to be fatal in the event that it’s swallowed or inhaled. This covers a wide variety of chemicals, including but not limited to turpentine, gasoline, and kerosene. All chemicals of this kind must be described with an SDS sheet.
Asphyxiating
An asphyxiant is a chemical that, when inhaled, deprives the body of oxygen. When it does this, it has the potential to lead to death. As such, asphyxiants must be designated with SDS sheets. Examples of asphyxiants include argon, nitrogen, methane, and helium.
Sensitizing
The last type of chemical we’re going to discuss is the sensitizing chemical. This is a chemical that spurs an allergic reaction in certain individuals. This can lead to a variety of health problems, including rashes, breathing issues, and more. Examples of sensitizing chemicals include formaldehyde, benzylic, and chromium.
How to Create an SDS Sheet
Now that we’ve discussed the importance of creating SDS sheets, and now that we’ve discussed what constitutes a hazardous chemical, let’s talk about how to make an SDS sheet. Generally speaking, creating an SDS sheet looks something like this:
Collect Data About the Product
First and foremost, you need to collect data about the product. This includes everything from the chemicals included to the amount of each chemical included and more.
You’re advised to follow the guidelines provided in OSHA Standards. This includes a 16-part table indicating the following:
- Identification
- Hazard Identification
- Composition
- First-aid Measures
- Fire-fighting Measures
- Accidental Release Measures
- Handling and Storage
- Exposure Controls
- Physical/Chemical Properties
- Stability and Reactivity
- Toxicological Information
- Ecological Information
- Disposal Considerations
- Transport Information
- Regulatory Information
- Additional Information
You can learn more about these guidelines by visiting the OSHA website and, in particular, this link.
Input Information
Once you’ve collected the necessary data, you’ll need to formally input it so as to create a legitimate sheet. This can be done either on a hard copy or through digital means.
If you’re using a hard copy, you’re advised to put it in a binder. If you’re using digital means, you’ll need to provide digital access to your employees.
Regardless, fill out each section of the table thoroughly. By filling out each section and subsection, you ensure that you don’t miss any important information. This helps you prevent fines.
Compare Your SDS Sheet to a Similar SDS Sheet
Once you’ve finished filling out your SDS sheet, you should compare it to a similar sheet from another organization. This way, you can determine whether you’ve left out any glaring pieces of information. You can also alter your SDS sheet to make it more refined and readable.
Note: when doing this, it’s best to compare your sheet to a sheet from a large and reputable organization. These organizations are bound to have the most legally airtight SDS sheets.
Post the SDS Sheet
Once you’ve compared your SDS sheet to a similar SDS sheet, and you’ve edited it for perfection, it will be ready to go. You can post it either in your digital database or in a binder in your workspaces.
If you have a compliance system in place, you should be sure to put the SDS sheet through this system to ensure that it’s met all criteria.
Tips for Maintaining SDS Sheets
Now that you see the importance of maintaining SDS sheets, you might be wondering: how do you go about maintaining SDS sheets so that you’re meeting compliance over time? There are several strategies you can utilize and we’re going to discuss them in detail below.
Read Through OSHA’s Hazard Communication Standard
First and foremost, you should read through OSHA’s Hazard Communication Standard. This is a set of guidelines indicating what companies must do in order to abide by OSHA hazardous material rules. These guidelines are integral to understanding hazard communication.
If you don’t read through this guide, you’ll miss out on the intricacies of hazardous communication rules. This will leave you prone to mistakes. You can find a summary of the Hazard Communication Standard by clicking here.
Designate an Employee to Facilitate a Hazardous Communication Program
Not only should you read through the Standard but you should also designate a specific employee to overtake your company’s hazardous communication program. This employee will focus primarily on ensuring that your company is meeting hazardous communication guidelines.
A large component of this task is managing safety data sheets. The employee in question will help devise a process for producing such sheets and will therefore systematize it. This individual should also create a training plan so that your employees can properly learn the ins and outs of SDS sheets as well as hazardous communication in general.
Create a Hazardous Communication Plan
The best way to go about managing an SDS system is to create a systematized plan. This way, you’ll have rules set for how to handle every new chemical that comes into the workplace. You’ll also have rules established for how and when to update existing SDS sheets.
Having this framework established enables you to regulate your SDS process so that you don’t make mistakes. It also ensures a thorough and robust SDS system, the likes of which can provide ample benefit to your employees.
Do you need assistance creating a hazardous communication plan? Check out this sample hazard communication program. published by the state of Texas.
Take Inventory of Hazardous Chemicals in Your Workplace
Next, you should take inventory of hazardous chemicals in your workplace. Make a database of each chemical, using its CAS registry number, in particular, to label it.
A CAS registry number is a number regulated by the Chemical Abstracts Service. This service attaches number codes to each chemical in existence, thereby allowing you to find them in SDS sheet databases with little trouble.
Label Containers That Hold Chemicals
You’re also going to want to label containers that hold chemicals. This way, you’ll know exactly what they consist of, regardless of whether you’re shipping them or using them in your workspace.
You don’t need to include all of the information that you’ll include on an SDS sheet. However, you should include things like chemical identifiers, hazard statements, and precautionary statements.
Create Safety Data Sheets
And now we’ll move on to the big step: creating safety data sheets. Use your catalogued chemicals to draw up the safety data sheets one by one. To keep things orderly, go by alphabetical order.
While there is some freedom about how to draw up a safety data sheet, you’re strongly advised to use the guidelines laid out by OSHA in its Occupational Safety and Health Standards. We reviewed those guidelines in-depth above.
Review Safety Data Sheets Every 3 Years
In addition to creating SDS sheets, you must also update SDS sheets. By law, this needs to be done every 3 years, or whenever new information becomes available about a specific chemical that you’re using.
When reviewing your SDS sheets, be sure to check existing information against new information. Then, add new information as needed. If you don’t update your SDS sheets in a timely manner, you won’t meet compliance. This will leave you vulnerable to legal penalties.
Add New SDS Sheets as Needed
Every time a new hazardous chemical comes into your workspace, you need to create an SDS sheet for it. There are no exceptions to this rule. Have the SDS sheet posted before using it and then update it over time as needed.
Utilize SDS Management Software
Years ago, you had to draw up SDS sheets by hand. These days, however, there is ample software available to help you with the task. This software not only provides you with templates for creating SDS sheets but it also allows you to seamlessly update and manage said SDS sheets.
In essence, it does all the hard work for you. So, if you want to keep your workload to a minimum, this is undoubtedly the way to go. Learn more about SDS management software by clicking here.
Outsource the Task
If you don’t have the time, wherewithal, or workforce necessary to maintain SDS sheets, you could instead just send the task off to an experienced SDS management company. These companies are specifically designed to maintain their clients’ SDS databases and will ensure that you’re meeting compliance at all times.
The website you’re visiting currently is a website for an SDS management company, KHA Online SDS. We offer software solutions for managing SDS sheets and make it extremely simple for you to maintain and update your SDS system.
Our software not only provides pre-made safety data sheets for a range of different chemicals but it also enables you to edit portions of these sheets so that they match with your company’s uses. This way, you can upload new safety data sheets in just a few minutes time, regardless of your technical expertise.
Our Online SDS software is used by companies in a variety of industries, from healthcare to manufacturing to chemical processing and more. It’s also used in a number of universities as well as on the municipal level.
If you’re looking to meet SDS regulations compliance, using our software is a great way to go. It simplifies the process and enables all employees to access SDS sheets with ease.
Need Help Managing SDS Sheets in Your Organization?
As you can see, SDS sheets are legally required in organizations that work with chemicals on a commercial basis. Failure to maintain SDS sheets can leave your business vulnerable to lawsuits and OSHA violations. Not to mention, it can endanger your employees.
That said, maintaining SDS sheets over time can be difficult. It can also be time-consuming. As such, you might be interested in outsourcing the task to an SDS management company.
If so, look no further than KHA. We’re a highly experienced SDS management company based out of Merrillville, Indiana and we offer one of the top online SDS management software on the market. It comes not only with online management capabilities but regulatory reports but multi-device use, offline backup, and much more.
Have any questions about our software or what we can do for your organization? Contact us now!