How to Improve Employee Health and Safety
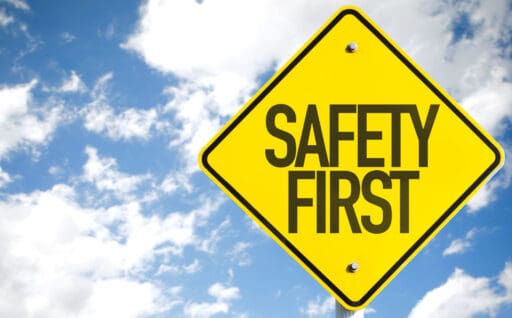
Did you know that there are about seven million non-fatal workplace accidents that occur every year? These accidents can lead to injuries that require time off of work and have lasting effects, no matter how serious.
Needless to say, workplace accidents are bad for businesses and even worse for employees. So, nobody wants workplace accidents to happen, which is why we are here to help.
Keep reading and learn how to improve employee health and safety inside and outside of your company.
Having Good Leadership
If you want to improve the health and safety of the company, you need to have someone high enough in your company to encourage others to follow that ideology. This is where a good leader comes in.
For any business to succeed, they need good leadership to push the rest of the employees in the right direction.
However, this is easier said than done for a company to have within its rank. Only about 10% of companies say that they have a strong leadership bench. On top of this, 77% of organizations in that link said that they have a leadership gap within their ranks.
Before you go rushing to conclusions, know that this is not always the employees’ fault. About 58% of managers in the survey above said that they had no proper training for the position that they took on.
What this means is that companies are having a hard time finding good leaders, but at the same time, those companies may not be presenting an encouraging climate for good leaders to thrive and stay in.
Figure out what you want in a leader and see if they can communicate with people while maintaining respect. Also, these leaders need to have a good work ethic and be invested in the ideology that they have with your company.
If you can successfully recruit good leaders for your company, you have a much better chance of promoting health and safety measures effectively within the ranks.
Having Proper Training
As mentioned above, more than half of the managers in that survey said that they had no proper training before taking on that position. Well, if you want to be a successful company that has organized protocols, that cannot be the case for your company.
You need to invest in proper training for your employees. This can start by simply taking upper management on a work trip to your company’s headquarters to go over these policies. Hire an experienced third party that is an expert in the field if that is what it takes to train your management.
Make sure that your leaders have this information down to a science and that they can adequately communicate and teach this knowledge to their fellow employees.
After that, they will report to their respective branches and have this seminar run with the employees that they manage. Dedicate an appropriate amount of time for employees to take all of this information in.
This is especially critical for new employees that may just be starting out not only in your company but possibly your industry. Have them start slow and make sure that your managers are keeping an eye on them and re-instating the healthy and safety in the workplace before they leave them be.
Have Noticeable Safety Reminders
Another way to enhance health and safety protocols in your company is by having visual reminders all around your workplace. Think about it. People are most likely going to walk around the same places in your office space or your factory every day if they work there.
Having those signs around your workplace can anchor their memory for them and make it a habit to consider those consequences or actions before something bad happens.
This method has proven very effective in getting people to remember a certain statement or message compared to just hearing about it. That is because humans generally cannot remember what they hear compared to what they see and what they read.
This study shows that humans only remember 10% of what they hear. So, if you are just giving these health and safety protocols in a seminar, you are going to be lucky if your employees remember a fraction of what goes on during that seminar.
Now, compare that to seeing the same thing every day. Humans remember 80% of what they see. So, by that statistic alone, humans are eight times more likely to take in the information that they have to see every day.
Post these safety reminders all around your workplace for employees to process the most important workplace safety information that you have for them.
Inspect Your Workplace
The next thing that you should do to make sure you have the right health and safety standards is to inspect your workplace.
This can be done in several ways. If you believe that everyone from management to employees is not following the protocols, you can have someone disguise as an employee and take notes of what is being followed, if anything at all.
However, this type of action goes further than negligence. You also need to inspect if the equipment that you are using is up to date and is working properly. If not, make notes of that and replace the equipment as soon as possible. In some cases, you may have to update the procedures you use for the whole area of the department.
Another example can be if you are using hazardous materials, what are you doing to protect yourself from those chemicals? Make sure people are wearing the proper safety equipment in this situation, such as gloves, masks, jackets, and more.
Doing proper inspections here will help your workplace run smoother, more efficiently, and most importantly, more safely.
Do not be afraid to acknowledge that some of your safety protocols and equipment could be out of date. If you discover that during an inspection, make sure to take action as quickly as possible.
Review Past Accidents Carefully
There is an old saying that if one does not learn from history, then they are doomed to repeat it. This is especially the case with workplace accidents because companies need to investigate these incidents to prevent them from happening again.
The truth is, there is not just safety on the line when it comes to reviewing these accidents. It can also cost a company a lot of money to pay for someone’s injuries that happened on their watch and can no longer work for them on top of that.
In 2019, there were about $171 billion in payments in the United States for people that had work-related deaths and injuries. If you do a little further math here, you will discover that that averages to over $1 billion per week.
This is why it is so important to take the time to investigate how an accident occurred and make sure that the story told from all sides of the incident checks out.
Let’s say that a machine malfunctioned and caused someone permanent nerve damage to their finger. Well, if you have camera footage and personal accounts from everybody in the room when it occurred, you may find out that someone turned their head away from the machine while it was operating.
In that situation, you can reinforce how important it is to keep your eyes on equipment like that that is operating at all times.
Make sure you have people on your investigative team who have the skills to read through the lines and are very observant. They can help you get to your bottom line and prevent another incident like that from happening faster.
Updating Tools and Equipment
As mentioned before, part of inspecting a workplace is making sure that the area has the proper tools and equipment needed to keep up with proper safety protocol. Well, part of this is also knowing when it is time to modernize tools and equipment to meet ever-changing needs.
One way you can do this is to research the average lifespan of a tool that you buy. This can be measured over the years or by how often and demanding the service needed from that tool is.
An example that you may be able to compare this situation to is by comparing it to a car that you buy. Some cars have an average lifespan of about 10-12 years.
However, some people have different uses for the same car. Normally, it can take about 200,000 miles before the car is considered no use to most people. However, some people may do this in five years, while others may not be able to drive this in 20 years.
Then, some people fail to keep up with basic maintenance like lights and brakes, while other people are on top of every little repair that a car needs.
These are the types of things that can make or break the lifespan of a tool. You need to be aware of what the expected lifespan is, how much use the equipment is getting on a daily or weekly basis, and if there is anything that you can change or maintain on your own to make the equipment last longer.
New and updated equipment can also help you reach your bottom line more easily by making production go faster and most likely have fewer overall issues with your equipment that you need to stop production for.
Update Meetings
Another thing that you need to stay on top of is constantly updating your employees on health and safety protocols in your company. Admittedly, this can be a difficult thing to balance because you do not want to take too much time out of production, and you do not want your employees getting too annoyed about it.
However, it is something that needs to be reinforced every once in a while, so it may be good to do a refresher seminar once or twice a year.
There may be situations where you need to do a meeting about health and safety even sooner than this. An example of this is if your company just had major updates or a major overhaul of your old health and safety protocols.
In that situation, you will need to get your employees up to date on the new standards as soon as possible. This will not only help your company stay efficient with your current procedures, but it could also help improve your employee safety immediately if these measures are made appropriately.
Promote Feedback
Finally, encourage employees to have an open dialogue about the current health and safety protocols that are put in place in your company. They can be the most useful people to talk to about this because, at the end of the day, they are the ones working with these policies every day.
If you talk to enough employees, you could discover a flaw in the protocols that you put in place for your company. Or, if you talk to a rising star in the company, they could suggest something to add to those measures that you may have overlooked.
Improve Employee Health and Safety
These are some of the biggest keys when it comes to improving employee health and safety. You need to be organized, have good leadership, good training, updated tools and protocols, plus provide an open dialogue for employees to weigh in.
If you do all of this, you should see workplace safety improve in no time.
Do you need help in this field? Message us today to see how we can help.