2023 OSHA Updates to Know
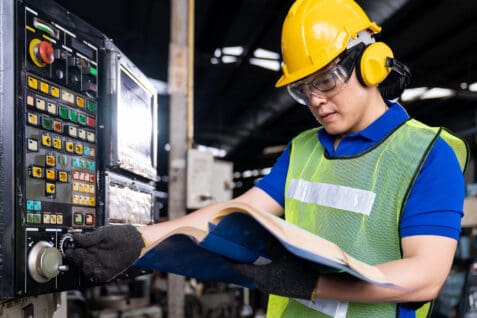
Last year was a busy one for the Occupational Safety and Health Administration (OSHA), with many new updates and enforcement protocols.
Obviously, that’s a good thing, since increased safety and health considerations are crucial to the well-being of employees and the overall success of a business enterprise. But it’s also tough to keep up with all the changing OSHA updates and regulations that affect your business.
That’s where we come in. In the following article, we’ll take a look at some of the most important OSHA regulatory updates for 2023, so you know what your business ought to be aware of. So, without further ado, let’s examine some of the main points and key takeaways from the new regulatory regime.
1. New Workplace Safety Plan
First up is the new workplace safety plan, which comes with stiff new OSHA penalties and citational schedules.
OSHA’s recent initiative, which was explained in this press release of January 26, is intended to be a “significant enforcement measure to discourage employers from disregarding their duties to protect employees and comply with OSHA guidelines and regulations.”
This OSHA compliance directive also applies to enforcement activities within the general industry, farming, maritime, and construction sectors. With a two-month lag time, the directive is intended to come into full effect by the end of March.
Let’s look at the two main components of the new strategy:
Instance-by-Instance Citations
The new regulations place particular emphasis on OSHA citations for instance-by-instance claims.
OSHA regional administrators and area directors can now issue fines for certain types of violations which they deem “instance-by-instance citations.” And that’s particularly the case where the agency identifies what they determine to be serious infringements of OSHA standards. It also applies to specific situations where the rule’s language allows a citation for each instance of noncompliance.
The press release explains that these circumstances include those related to lockout/tagout, machine guarding, respiratory protection, falls, and certain violations concerning OSHA recordkeeping. The reason for the rules changes is to make sure OSHA personnel are using the “full” capacity of the OSH Act when greater punishments are needed to discourage illegal behavior.
OSHA’s January 26 memorandum clarifies that case-by-case citations will only be issued if the new regulations permit it. That means they can be issued, for example, per machine, work area, entrance, or worker, as well as when violations can’t be resolved through a single method.
The press release also instructs inspectors to carefully document each violation if an inspection may lead to instance-by-instance violations.
Employers Are Encouraged Not to Group Citations
The second aspect of OSHA’s new memorandum encourages regional administrations and area directors to not group citations together.
Instead, OSHA instructs employers to better comply with the OSH Act through issuing individual citations. It’s a small change, but one that the agency feels is an important one. The OSHA updates also state that “violations that are proposed as instance-by-instance citations should not be combined or grouped.”
2. New Recordkeeping Rule
Recordkeeping is always an important aspect of OSHA compliance and mitigating OSHA penalties and citations.
That’s why it’s so critical to stay on top of their new recordkeeping rules, which seem to change with little notice. Take the newest change, for instance. Last year, OSHA released a Notice of Proposed Rulemaking (NPRM). This notice greatly alters the electronic injury and illness reporting requirements for many US workplaces. Here’s a look at how the requirements in this notice could affect your business:
The Expansion of Reporting Requirements
The NPRM requires that firms with at least 100 employees in certain selected industries electronically submit data from their OSHA Forms 300, 301, and 300A to the agency on an annual basis. It goes without saying that it’s a significant expansion of reporting needs for many businesses.
As far as the industries affected, these are listed in Appendix B to subpart E of the Recordkeeping Standard. Basically, enterprises with 100 or more employees in the listed industries are now also required to submit data from their Forms 300 and 301.
Data Publication
The Notice also states that OSHA will make public all the data it acquires through these reporting requirements.
Don’t get too concerned, however—the agency will remove any identifiers like names and contact info prior to releasing the data. There were many objections to this requirement in the Notice, but it’s going through anyway—that’s just how the Federal government works.
300A data from establishments that are presently under electronic reporting demands only contains general information about a certain amount of injury and illness occurrences. The 300 and 301 forms much more detailed information about individual cases, and this could include personally identifiable information. People are understandably anxious about the possibility of completely deleting any potential identifying info from these documents and about how to make sure that confidential data remains shielded.
3. New Hazard Communication (HazCom) Standard
The Hazard Communication (HazCom) Standard is one of the most significant and far-reaching of the OSHA updates and new regulatory rules.
Recently, OSHA released an update—one that was long in coming—to the HazCom Standard. Most importantly, the change aligned it with the seventh edition of the United Nations’ Globally Harmonized System (GHS).
So what does that mean for businesses? In truth, it means a lot of important updates, including revised classifications for combustible vapors, aerosols, modified requirements for shipped containers, and revised transportation demands for bulk shipments. Basically, the new OSHA regulatory updates require substance manufacturers to comply with a whole slew of new safety and compliance measures.
The Alterations
The alterations being proposed would have broad repercussions for the entire chemical supply chain, mainly for the producers of relevant chemical items. Consequently, OSHA got plenty of input from stakeholders before the public comment window closed in May of 2021. OSHA also organized a public hearing in late September of that year, to offer an opportunity for stakeholders who had registered a Notice of Intent to Appear before the deadline to provide further remarks.
The Regulatory Agenda for 2022 required that OSHA publish their HazCom update at the end of 2022. And since the period for compliance begins as soon as the update is published, it’s up to businesses to now ensure this is the case in 2023.
We will have to wait for the finalized rule to determine if OSHA has adjusted the timeline of the Notice of Proposed Rulemaking (NPRM), as many industry members at the 2021 public hearing mentioned that the timeline for both substance and mixture producers was too short. It is certain, however, that big modifications are on the way and those in the chemical supply chain must get ready.
4. Updated Silica Rules
OSHA also has updated and changed its existing Respirable Crystalline Silica (RCS) regulation.
There’s a lot to unpack here, as they say. Back in 2016, OSHA established two new standards for RCS, one for the general industry and maritime (29 CFR § 1910.1053) and another one for construction (29 CFR § 1926.115). The 2016 standards incorporated a new Exposure Action Level (AL) of 25 µg/m3 and reduced the Silica Permissible Exposure Level (PEL) from 100 to 50 µg/m3.
The standards also include regulations on installing exposure controls, carrying out medical surveillance programs to monitor exposure to RCS, and maintaining a written exposure control plan.
The rulemaking proposed by OSHA will have a major influence on the industries it affects, such as many cement and asphalt factories and building sites. In relation to OSHA’s Recordkeeping Standard, medical removal incidents are seen as recordable injuries, either categorized as “time away from work” or “limited activity” depending on the decision of the employer, whether to completely remove the employee from the worksite or just change their duties in order to reduce silica exposure.
Businesses affected by the silica regulations must be sure to have a thorough workplace assessment and industrial health monitoring regimen in place, as well as a reliable incident management system to guarantee the swift recording of medical removal cases.
5. The Lockout-Tagout (LOTO) Update
Finally, let’s take a look at OSHA’s “Lockout Tagout” (LOTO) rule, which is officially called the “Control of Hazardous Energy” standard.
Innovative technologies like computer-based safety controls are now known and incorporated into various hazardous energy control standards around the world. Even so, the laws of 29 CFR 1910.147 have remained largely the same for roughly four decades.
For some time, OSHA has discussed the potential requirement for a revision, and in May 2019 made a Request for Information (RFI) to get intel from stakeholders on the pros and cons of modern technology for controlling hazardous energy. The RFI of 2019 points out, for instance, that the LOTO standard currently stipulates that control circuit devices cannot be used as energy-isolating devices, however, “the agency acknowledges that recent technological advances may have enhanced the safety of control circuit-type devices.”
The Spring Regulatory Agenda affirms that OSHA has considered all the comments received during the RFI process, and is now ready to begin the process of revising the LOTO standard. A notice of proposed rulemaking is slated to be released by March 2023. This decision will certainly have a widespread effect as the LOTO standard applies to a wide range of industries.
In other words, employers must take care to be aware of OSHA’s modifications and the consequences they may have on job safety and regulatory compliance.
How to Improve Your Compliance With OSHA Updates
Okay, so now that we know about some of OSHA’s regulatory updates, what can your business do to improve its compliance measures?
There’s a lot to prepare for to avoid OSHA penalties, but there are a few steps you can take that will help you avoid the wrath of the Federal government. Let’s take a look at some of easiest ways to do so:
Better Inspection Programs
Looking at different standards and regulations, it’s obvious that inspections are a major factor.
The Lockout/Tagout standard requires inspections to be done periodically to ensure all energy control procedures are in order. The silica rule also requires that employers do “frequent and regular inspections” of areas that fall within the rule’s regulatory sphere.
Better Incident Management
OSHA recordkeeping updates mandate that businesses begin electronically submitting data from Forms 300 and 301. So it helps to devise simpler methods of recording all accidents and illnesses in the workplace, as well as storing the documents in one place. It’s also best to fall into the habit of completing all mandated OSHA forms.
Use Data to Improve Decision-Making
To remain aware of the regulatory environment, which seems to change with increasing frequency, you need to be able to stay flexible and adapt to changing circumstances.
This is why it’s essential to be able to easily access safety data so you can monitor progress, adjust tactics when needed, and create more informed choices for ongoing development. Resources like our Online SDS will let you easily index data, compile regulatory reports, and archive data sheets, all from a personalized dashboard.
Get Ahead of the new OSHA Regulatory Updates by Using KHA Online SD
Every time new OSHA updates appear, it means a great deal of stress and bother for businesses to maintain compliance.
But it doesn’t have to. At KHA Online SDS, we specialize in providing Safety Data Sheet management, as well as offering workplace safety and health solutions. Plus, our Online SDS system furnishes you will all the support you’ll need to handle the most important safety and health matters, as well as stay ahead of OSHA’s next enforcement and regulatory updates.
So what are you waiting for? Contact us today to see how we can help you manage all your OSHA regulatory compliance needs.