Three Tips for Managing Chemical Inventory
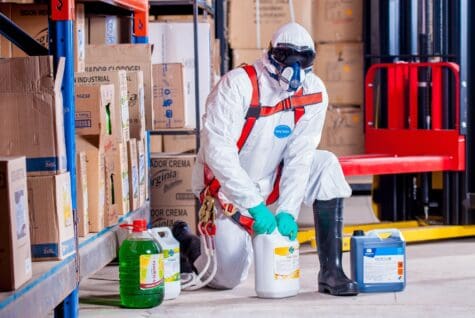
Did you know that 424,360 employees were nonfatally injured by chemical hazards in 2020? These figures from the last available year don’t even account for the hundreds of people that died as a result of chemical-related workplace accidents.
Employee exposure to harmful substances can kill those who work for you (and land you with hefty fines and lawsuits). That’s why chemical inventory management needs to be a top priority. Read on for three of the most important tips that you need for managing hazardous materials.
1. Manage Documents the Right Way
A good virtual document management system is essential for every facility that handles hazardous materials. This means getting an SDS technology that ensures compliance with OSHA regulations.
KHA’s SDS management software, HazMat Inventory application, and other tools allow you to collect data via images and create a list of all known chemicals. All you need to do is take a high-resolution image of a given label or chemical container. The application will automatically put these images into your inventory system.
You can also use this virtual storage system to create, update, and manage SDSs. Previously-inputted information will be saved to the system so that you do not need to type it out again whenever updates are necessary.
You can also re-use information from SDSs when creating sheets for new, similar chemicals. This will make the inventory process both smoother and more efficient.
2. Train and Assist Your Staff
Once you have safety data sheets and chemical labels, you’ll need to make sure it’s accessible to your staff. OSHA requires that SDSs are accessible in all areas of your facility. Employees also can peruse them from mobile devices assuming that you have a good online system.
Make sure that employees know where and how to access this information. Test them on whether or not they can correctly interpret the data after finding the forms (and train them appropriately if they cannot).
You also should teach them how to handle materials safely. This includes considering what will happen if exposure takes place- the point is to be prepared. Make sure that you also have backup plans for storage and handling in the event of natural disasters or power outages.
3. Keep Things Up to Date
OSHA requires all safety data information to be up to date. This means reviewing information for existing chemicals every 3 years to make sure that the information is still accurate. However, more frequent reviews can help to familiarize you with the materials as much as possible and ensure that information is updated.
If new chemicals arrive at your facility, SDSs need to update within 3 months. Labels must be revised within half a year. It’s important that you create a system for updating SDSs so that the process runs smoothly within your software.
Get Started With Chemical Inventory Management
Keeping track of hazardous materials in the workplace can be a challenge. Luckily, fully-managed chemical inventory tools make it easier to track, define, categorize, and learn about these dangers than ever before.
Now that you know how to keep yourself and your employees safe, it’s time to get started. Contact our SDS management professionals with any remaining questions that you have and to get started with our safety data services.