OSHA Inspection List – Be 100% Prepared
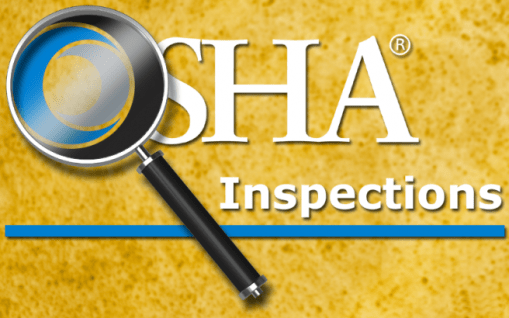
Their job is to ensure the health and safety of all employees at your facility and regulate the occupational safety standards that help to reduce your company’s accidents on the job. It’s no surprise that OSHA, can and will, show up from time-to-time to ensure that your facility is in regulatory compliance. Unexpected visits can make for a stressful day on the job, but it doesn’t have to be that way! Ever heard the saying “An ounce of prevention is worth a pound of cure.”? Follow these recommendations to help you be 100% prepared for an OSHA inspection.
NOTE: This list is not meant to be all-inclusive. You should refer to OSHA for complete lists of standards that apply to your specific work situation.
Employer Postings
- Make sure the required OSHA workplace poster is displayed in a high visibility area where all employees can access.
- The Summary of Occupational Illness and Injuries (OSHA form 200) should be posted in the month of February.
- Make sure all emergency telephone numbers are posted in a high visibility area that is accessible to everyone in the case of emergency.
Recordkeeping
- All operating permits and records should be up-to-date for items including elevators, air pressure tanks, and liquefied petroleum gas tanks.
- Employee training records should be accessible for review by employees.
- Employee medical records and records of employee exposure to hazardous substances should be up-to-date and in compliance with current standards.
Health and Safety Program
- There should be an active program in place that is concerned with general safety and health as well as the management of hazards specific to the worksite. In addition, there needs to be one person that is clearly responsible for the overall activities of the program.
- Within the program, you should have procedures in place for handling in-house complaints regarding safety and health.
- Communicate with your employees about what accomplishments your health and safety program has made in ensuring a safe workplace for all.
Medical Services and First Aid
- All employees who are expected to respond to medical emergencies in the workplace as part of their work must have the following:
- First Aid Training
- Hepatitis B vaccination
- Appropriate training on procedures to protect them from bloodborne pathogens
- Have appropriate PPE available to them
- First Aid Kits are easily accessible to each work area, with necessary supplies available, periodically inspected and replenished as needed.
- Eye Washing and quick Drench Shower stations are available and easily accessible in areas where corrosive liquids and materials are handled.
Fire Protection
- Test your fire alarm regularly; at least on an annual basis.
- Inspect your fire doors to ensure they are in good operating order and are free from obstructions.
- Make sure portable fire extinguishers are readily accessible throughout your facility and are recharged regularly and noted on the inspection tag.
Personal Protective Equipment
- You should select and have the affected employees use properly fitted PPE suitable for protection from hazards.
- All PPE must be maintained in a sanitary condition and ready for use.
- As an employer, make sure your staff is trained on PPE procedures.
General Work Environment
- All work areas should be clean, sanitary and orderly.
- All work areas should be adequately illuminated.
- Evaluate all confined spaces for compliance with 29 CFR 1910.146
Walkways
- All aisles and walkways are clear of obstructions and debris.
- Any wet surfaces should be covered with non-slip materials.
- Make sure there is safe clearance for walking in aisles where motorized or mechanical equipment is operating.
Exiting or Egress
- All exits must be marked with an exit sign and illuminated by a reliable light source.
- Any doors, passageways or stairways, that are not exits or access to exits must be labeled as such (“NOT AN EXIT”, “TO BASEMENT”, “STOREROOM”, etc.).
- Keep all exits free from obstructions and debris.
Portable Ladders
- All ladders should be maintained in good working order; all moving parts should operate freely without binding and all joints between steps and side rails are tight.
- Employees should be prohibited from using broken ladders or other defective equipment.
- Make sure your employees have access to proper ladder safety training.
Hand Tools and Equipment
- Ensure your employees are knowledgeable of the hazards created due to faulty or improperly used hand tools.
- Make sure all tool handles are wedged tightly in the head of the tool.
- Maintain cutting edges on tools to keep them sharp to prevent binding or skipping.
Power Tools and Equipment
- Make sure all grinders and saws have the appropriate safety guards in place.
- All power tools must be used with the correct shield, guard, or attachment recommended by the manufacturer.
- All rotating or moving parts of equipment must be guarded to prevent physical contact.
Machine Guarding
- Implement a training program to instruct employees on safe methods of machine operation.
- Conduct regular safety inspection of machinery and equipment.
- Make sure all emergency stop buttons are colored red.
Lockout / Tagout
- Identify all appropriate electrical enclosures.
- Ensure that appropriate employees are provided with individually keyed personal safety locks.
- In the event that equipment cannot be shutdown, locked-out and tagged, make sure you have a procedure in place to address this situation and rigidly adhere to it.
Industrial Trucks / Forklifts
- Only trained employees should have access to operate such equipment.
- Regularly inspect the brakes to ensure the industrial truck can safely come to a complete stop while fully loaded.
- Each industrial truck must have a warning horn, whistle or other device which can be clearly heard above the normal noise within the areas of operation.
Entering Confined Spaces
- Perform the appropriate atmospheric tests for oxygen deficiency, toxic substances and explosive concentrations in the confined space before entry.
- Choose a competent entry attendee on standby, trained and equipped to handle an emergency.
- Adequately illuminate the confined space for the work to be performed in a safe manner.
Environmental Controls
- Instruct employees proper first-aid and other emergency procedures.
- Ensure employees are aware of the hazards involved with the various chemicals they may be exposed to in their work environment.
- Use wet methods to prevent the emission of airborne asbestos fibers, silica dust and similar hazardous materials.
Flammable and Combustible Materials
- Store all combustible scrap, debris and waste materials in covered metal receptacles and promptly remove from the worksite.
- Only use approved storage containers and tanks when storing and handling flammable and combustible liquids.
- “NO SMOKING” signs must be posted in areas where flammable or combustible materials are used or stored.
Hazardous Chemical Exposure
- If hazardous substances are used in your processes, you should have a medical or biological monitoring system in operation.
- Use a vacuum, rather than blowing or sweeping dusts whenever possible.
- Institute control procedures for hazardous materials, such as respirators, ventilation systems and handling practices.
Hazard Communication – HazCom
- Make sure you have a hazard communication program in place that deals with Safety Data Sheets (SDS), labeling, and employee training.
- Ensure that every employee has access to Safety Data Sheets for each hazardous substance in use within your facility.
- Provide HazCom training to all employees.
Noise
- Provide proper PPE in the workplace where noise levels exceed 85dBA.
- Engineer controls to reduce excessive noise levels. Administrative controls can be used where engineering controls are deemed not feasible.
- Provide periodic audiometric testing to employees to ensure you have an effective hearing protection system.
Identification of Piping Systems
- When the contents of pipelines are identified by name or name abbreviation, make sure the information is readily visible on the pipe near each valve or outlet.
- When pipelines are identified by color, clearly post the color code at all locations where confusion could introduce hazards to employees.
- Post suitable warning signs or tags when pipelines are heated by electricity, steam or other external source. Ensure the signs or tags are place at unions, valves, or other serviceable parts of the system.
Again, this list was not intended to be all-inclusive. You should always refer to OSHA for complete lists of standards that apply to your specific work situation. However, we hope this gives you a good starting point to get your facility on track for your next inspection. Stay safe out there!